04
2025
--
03
Análisis completo de las diez preguntas más comunes sobre los barriles abiertos: la guía definitiva para resolver problemas desde fugas hasta deformaciones.
¿Por qué siempre hay fugas en los barriles abiertos durante el transporte? ¿Por qué los barriles de plástico reutilizados se agrietan en menos de medio año? Como profesional de la industria del plástico con 15 años de experiencia, he sido testigo de innumerables clientes que han perdido decenas de miles de yuanes por ignorar "pequeños problemas".
Este artículo se basa en la retroalimentación práctica de más de 200 fábricas en todo el mundo, recopilando10 principales puntos de dolor en el uso de barriles abiertos— Desde fallos de sellado, colapsos por apilamiento, hasta desprendimiento de etiquetas y residuos de olores, cada problema ofrecesoluciones sencillas, ayudándote a evitar riesgos y reducir costos de comunicación internacional.
Ya seas un principiante en compras o un gerente de logística experimentado, dedica 3 minutos a dominar estos consejos y ahorra al menos 1 año de tiempo de prueba y error!
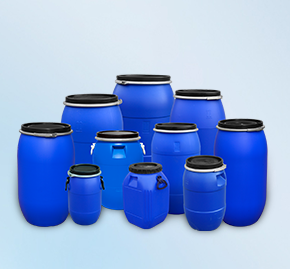
1. Problema: La tapa del barril no sella correctamente, lo que provoca fugas
Causas del problema:
①Compatibilidad química insuficiente del anillo de sellado:
Por ejemplo: el anillo de sellado de EPDM se hincha al entrar en contacto con aceites minerales (tasa de expansión de volumen > 15%), mientras que el caucho fluorocarbonado (FKM) puede resistirlo pero cuesta 3 veces más.
Norma de la industria: debe referirse a la "Tabla de compatibilidad química" certificada por la ONU (como ISO 1629).
②Tolerancia de procesamiento de roscas excedida:
El error de paso de la rosca del borde del barril es > 0.3mm (requisito estándar ≤ 0.1mm), lo que provoca un acoplamiento inadecuado.
Común en barriles de bajo precio que utilizan moldes de baja precisión (vida útil del molde < 100,000 ciclos).
③Deformación por tensión térmica:
El coeficiente de expansión lineal del HDPE es 1.5×10⁻⁴/°C, el de la tapa metálica es 1.2×10⁻⁵/°C, y con una diferencia de temperatura de 50°C, la diferencia de diámetro puede alcanzar 1.2mm.
Soluciones:
Reemplazar el anillo de sellado resistente a la corrosión química.
Asegurarse de que la tapa del barril esté apretada en orden diagonal.
2. Problema: Deformación o hundimiento del cuerpo del barril
Causas del problema:
①Superación del umbral crítico de vacío negativo:
La resistencia al vacío del barril de HDPE es aproximadamente -0.5bar, si la presión de vapor del líquido es demasiado alta (como la gasolina a 40°C con presión de vapor > 0.8bar), el cuerpo del barril colapsa al enfriarse.
②Concentración de carga dinámica:
Cuando el área de contacto del brazo de la carretilla elevadora es solo de 50cm², la presión local = carga / área (por ejemplo, 500kg/50cm²=10kg/cm²), superando la resistencia a la compresión del HDPE (8-12kg/cm²).
③Pobre estabilidad térmica de los materiales reciclados:
Los barriles que contienen más del 30% de material reciclado tienen una temperatura de deformación térmica (HDT) que baja de 75°C de HDPE puro a 60°C, lo que facilita la suavización a altas temperaturas.
Soluciones:
Evitar la exposición prolongada a ambientes superiores a 50°C.
No apilar más de 3 capas y agregar materiales de amortiguación.
3. Problema: Agrietamiento o fragilidad de los barriles abiertos
Causas del problema:
①Ruptura de la cadena de oxidación UV:
El HDPE rompe su cadena molecular bajo luz ultravioleta (longitud de onda 290-400nm), y la resistencia al impacto disminuye de 60kJ/m² a <20kJ/m².
②Transición de fragilidad a baja temperatura:
La temperatura de transición de fragilidad del HDPE es aproximadamente -70°C, pero al contener material reciclado, sube a -20°C, lo que facilita el agrietamiento en regiones frías.
③Defectos en el proceso de fabricación:
Una temperatura de inyección <200°C provoca mala fluidez del material fundido, dejando tensiones residuales en la pared del barril (valor de tensión >10MPa).
Soluciones:
Elegir barriles de HDPE que contengan aditivos anti-UV.
Evitar golpes bruscos antes de su uso en regiones frías.
4. Problema: Residuos difíciles de limpiar dentro del barril
Causas del problema:
①Diferencias de polaridad en la adsorción superficial:
La energía superficial del HDPE es baja (31mN/m), y las sustancias no polares (como grasas) se adsorben fuertemente a través de fuerzas de Van der Waals, requiriendo disolventes polares (como soluciones alcalinas) para romperse.
②Efecto de retención de microporos:
La porosidad del HDPE es del 0.01%-0.1%, y los residuos con un peso molecular <500Da (como colorantes) penetran en los microporos, requiriendo enjuague a alta presión (>5bar).
③Residuos de cristalización química:
Después de haber contenido soluciones saturadas (como jarabes), se forman núcleos cristalinos en la pared del barril (tamaño de cristal >10μm), que no se pueden eliminar con un lavado normal.
Soluciones:
Remojar con agua caliente + detergente alcalino y luego enjuagar.
Usar bolsas de revestimiento especial para prevenir residuos.
5. Problema: Rodamiento o desplazamiento del cuerpo del barril durante el transporte
Causas del problema:
①Defecto en el diseño del centro de gravedad:
La proporción de altura y diámetro del barril está desequilibrada (por ejemplo, altura > 1.5 veces el diámetro), la fuerza centrífuga al girar supera la fuerza de fricción en el fondo del barril (el coeficiente de fricción debe ser ≥0.4).
②Falta de dispositivo de fijación:
No se utilizaron correas de sujeción estándar ISO (resistencia a la tracción ≥2500kg) o almohadillas antideslizantes, lo que provoca un desplazamiento bajo la fuerza inercial (fórmula: F=m×a).
③Ángulo de apilamiento incorrecto:
Al apilar en múltiples capas, no se siguió la estructura "en pirámide", lo que provoca un desplazamiento del centro de gravedad y deslizamiento lateral.
Soluciones:
Utilizar correas o palets para fijar y rellenar los espacios vacíos.
Se recomienda elegir barriles con fondo antideslizante.
6. Problema: Olores extraños en el barril después de un almacenamiento prolongado
Causas del problema:
①Efecto de penetración de microporos:
La porosidad del material HDPE es >0.01%, los compuestos orgánicos volátiles (COV) se adsorben a largo plazo en los microporos de la pared del barril.
②Crecimiento de biofilm:
Los azúcares o grasas residuales (como los barriles de grado alimenticio) fomentan el crecimiento de moho cuando la humedad >60%, liberando olores sulfurosos.
③Residuo de detergente:
Los detergentes altamente ácidos (pH <3) corroen la superficie de plástico, formando superficies rugosas que adsorben moléculas de olor.
Soluciones:
Sumergir en una solución de vinagre blanco o bicarbonato de sodio durante 24 horas.
Secar completamente y ventilar antes de almacenar.
7. Problema: Etiquetas caídas o información borrosa
Causas del problema:
①Mala resistencia a la intemperie del material de la etiqueta:
Las etiquetas de papel comunes se desprenden cuando la humedad >80% o la temperatura >40°C debido a la expansión de las fibras.
②Incompatibilidad del adhesivo con el plástico:
La energía superficial del HDPE es baja (aproximadamente 31 dyn/cm), se requiere un adhesivo acrílico especial (fuerza de unión ≥3 N/cm²).
③Contacto con solventes:
Los líquidos de tipo cetona (como la acetona) disuelven la tinta de la etiqueta (parámetro de solubilidad >20 MPa¹/²).
Soluciones:
Utilizar etiquetas impermeables de grado industrial o identificación grabada con láser.
Limpiar el cuerpo del barril y aplicar una imprimación (como limpiar con alcohol) antes de pegar.
8. Problema: Desgaste de la rosca después de reutilizar
Causas del problema:
①Acumulación de estrés por fatiga:
La resistencia a la flexión de la rosca de HDPE es de aproximadamente 25MPa, la apertura y cierre frecuentes (>50 veces) provocan la expansión de microfisuras.
②Fricción entre metal y plástico:
La rosca de la tapa metálica (rugosidad Ra > 1.6 μm) acelera el desgaste del plástico, y los fragmentos atrapados agravan el daño.
③Influencia de la temperatura:
A bajas temperaturas (<10°C), la fragilidad del HDPE aumenta, lo que facilita la ruptura de la rosca.
Soluciones:
Aplicar regularmente grasa de silicona de grado alimenticio para proteger la rosca.
Reemplazar la tapa del barril después de un solo uso (para escenarios de alta frecuencia).
9. Problema: Insuficiente capacidad de carga en el fondo del barril abierto, lo que provoca el colapso del apilamiento
Causas del problema:
①Insuficiente rigidez anular:
El diseño del fondo no pasó la prueba ASTM D2412 (rigidez anular ≥8 kN/m² es calificado).
②Impacto de carga dinámica:
La presión instantánea al manipular con carretilla elevadora supera la carga estática (por ejemplo, la carga estática de un barril de 200L es de 1 tonelada, mientras que la dinámica es solo de 500kg).
③Contaminación por material reciclado:
La adición de material reciclado >30% reduce la resistencia a la compresión (la resistencia a la compresión del HDPE puro es ≈28MPa, mientras que la del material reciclado es ≈18MPa).
Soluciones:
Elegir barriles con diseño de "fondo anular grueso" (reforzar el soporte).
Al apilar, colocar los barriles pesados abajo y los ligeros arriba.
10. Problema: Fugas de líquido en el barril debido a la expansión por diferencias de temperatura
Causas del problema:
①Diferencias en el coeficiente de expansión volumétrica:
El coeficiente de expansión del líquido (como el agua) es ≈0.00021/°C, el coeficiente de expansión del barril de HDPE es ≈0.00015/°C, con una diferencia de temperatura de 30°C, la diferencia de volumen es >2%.
②Obstrucción del orificio de ventilación:
Los orificios de ventilación temporales de menos de 5 mm son fácilmente obstruidos por líquidos de alta viscosidad (como grasas), y pueden explotar cuando la presión interna >0.1MPa.
③Fallo de elasticidad del sellado:
A bajas temperaturas, la dureza de los anillos de sellado de EPDM aumenta (de 50 Shore A a 70 Shore A), perdiendo la capacidad de sellado por rebote.
Soluciones:
No llenar más del 90% del volumen del barril.
Usar tapas temporales con orificios de ventilación en ambientes de alta temperatura.
Independientemente de si se trata de fugas, deformaciones o problemas de limpieza,barril abierto.Cada detalle afecta directamente la seguridad del transporte y los costos operativos. Este artículo se basa en casos reales y parámetros técnicos en la cadena de suministro global, desde la ciencia de materiales hasta las normas operativas, para desglosar las raíces de los riesgos y ofrecer soluciones prácticas y aplicables. Si necesita asesoramiento personalizado, no dude en contactarnos por mensaje privado: ¡deje que la experiencia profesional se convierta en su cortafuegos contra riesgos!